Indoor vertical farming represents one of relatively fresh approach to food production. Scenarios of plant factories producing fresh greens year-around close to consumers have been published in media and they have raised not only the interest among consumers but also the interest among investors. In 2017, Plenty, a company producing vertical farming facilities, raised an investment of $200 million USD which is the largest funding in history in agriculture technology. In the scientific community, vertical farming seems to be a slightly contradictory topic due to multiple different approaches. The aim of this study was to assess vertical farming from the perspective of resource efficiency.
What is vertical farming?
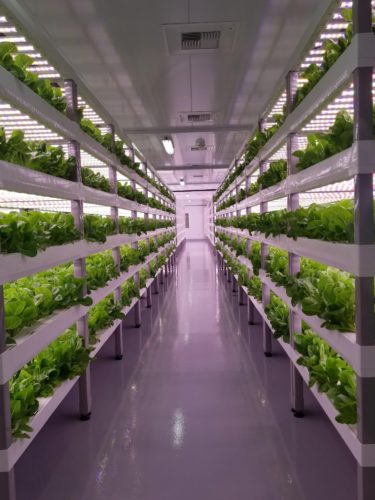
Vertical farming (VF) is originally defined as a practice of cultivating crops vertically and it can be applied outdoors and indoors. However, the modern idea of vertical farming utilizes highly controllable indoor premises equipped with growing beds, LED lights and irrigation system for providing plants water and nutrients. The growing beds can be either stacked horizontal beds, vertical towers or vertical cylinders which placed as densely as possible to maximize the yield per area but also considering lighting, air rotation and harvesting. In Figure 1 is a typical indoor vertical farm equipped with stacked growing beds.
Soilless cultivation
The cultivation method used typically in indoor vertical farms is called hydroponic cultivation. It is a so-called landless cultivation method which is using aggregate materials instead of soil and therefore the plants are taking nutrients and water through the material such as. peat, rock wool or gravel. Advantages of hydroponic cultivation are the efficiency of water and nutrients use and controllability. Being combined with a highly controlled cultivation room, the water evaporating from the plants can be recovered in the air condition system where the condensed water is recirculating back to the irrigation system. Thus, in theory, the water use efficiency of indoor vertical farming is 100%.
Energy from LED-lights
One significant difference between conventional greenhouse cultivation and VF lies on the source of the light. Conventional methods are utilizing solar radiation mainly to perform photosynthesis while VF is utilizing artificial lighting only. Therefore, VF is basically not dependent on the location and the climate conditions of the farm, unlike greenhouses which energy consumption is highly depending on the available amount of sunlight and climate conditions. In literature, also VF systems utilizing the solar light are discussed but this study is focusing only on the VF systems utilizing artificial lighting only.
In the 21st century, lighting technology has taken a huge step forward in terms of energy efficiency. During the last 10 years, light emitting diodes (LED) have replaced high-pressure sodium lamps and fluorescent lamps due to the improved conversion efficiency from electricity to visible light. In plant cultivation, the usable spectrum of for plants is from 400nm to 700nm and this range is called as photosynthetically active radiation (PAR). Currently, the most efficient LED lights designed for plant cultivation are converting around half of the electricity to PAR. The rest of the energy is converting to heat and therefore VFs do not require heating even in northern locations but cooling instead.
Inefficiency of photosynthesis
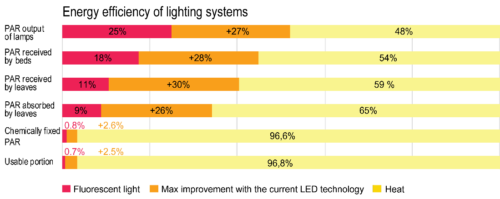
As around half of the energy intake of the LED converts to PAR, only a small fraction of that ends up to the plant itself. The efficiency of converting electricity to chemical energy of a plant is called as photosynthetic efficiency. Due to the multiple reactions and losses in the reaction chain of photosynthesis the total photosynthetic efficiency is only a few per cent for most of the plants. In Figure 2 is shown an approximation of the losses in the reaction. Based on the figure, currently, the best achievable photosynthetic efficiency for a VF system is 2.5%.
Life cycle assessment
Life cycle assessment (LCA) is a tool developed for analyzing the environmental impacts of products and processes comprehensively. Through its life cycle from raw material acquisition through production, use, end-of-life treatment, recycling, and final disposal (Kozai et al. 2016; International Organization for Standardization, 2006). The procedure of ISO-standardized LCA is shown in Figure 3.
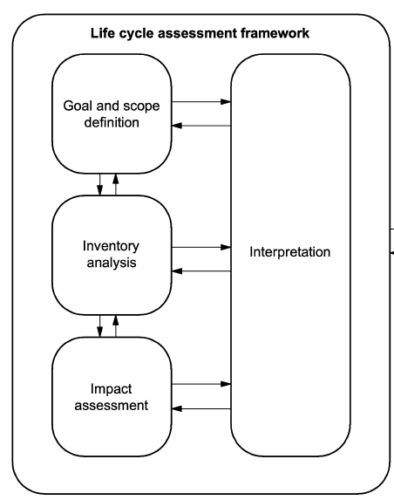
In the study, the goal was to conduct a comparative LCA on vertical farming and conventional greenhouse farming and figure out whether vertical farming could be a feasible technology for growing crops primarily for human food or animal feed.
In the scope, the functional unit is defined as well as the system boundary and impact indicators used for the assessment. In most of the studies discussing vertical farming, the functional unit is defined to be 1 kg of dry or fresh lettuce. Due to the slight variation of the dry matter content of lettuce in the literature, this study is performed with the functional unit of 1 kg of dry lettuce. The system boundary is defined as shown in Figure 4. Based on the literature, the cultivation process is clearly the most resource-intensive phase of a life cycle of lettuce from the perspective of energy, water, land and fertilizers. Thus, the study is excluding other processes but the energy production and the cultivation. In order to assess the processes from different perspectives, the study applies multiple indicators: Global Warming Potential (GWP), Water Footprint (WFP), fertilizers use and land use.
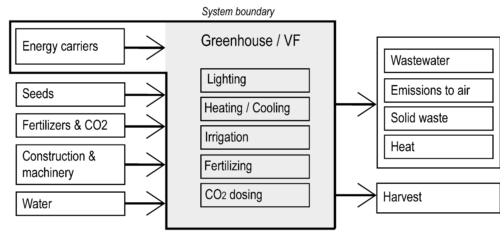
Data acquisition
Due to the limited amount of VF in operation, this study is applying background data gathered from the literature and mainly from three studies discussing vertical farming from the perspective of resource use efficiency: Kozai (2013), Kikuchi et al. (2018) and Graamans et al. (2018). The studies provide data for energy, water and land use based on existing vertical farm and modelling.
Environmental impacts of vertical farming

Figures 5, 6 and 7 show the global warming potential (GWP) of the greenhouse gas (GHG) emissions emitted by VFs and greenhouses with different LED efficiencies,
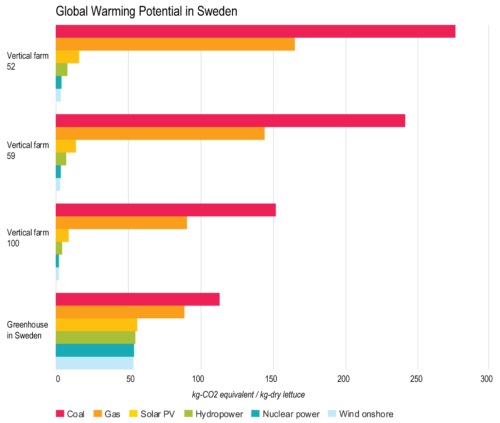
(2014).
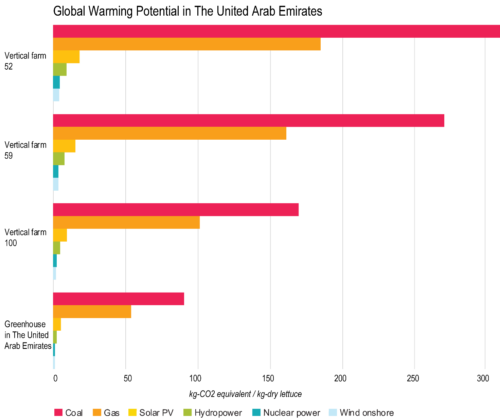
energy sources, and different locations. All the figures show the huge difference of GHG between coal and natural gas, and the other sources: a VF supplied with coal energy has about 80 times higher GHG emissions compared to a VF supplied with wind or nuclear power which represent the least GHG emitting sources. From the perspective of energy sources, the greenhouses in Sweden and the Netherlands are exceptional since the fraction of the heating with natural gas represents the majority of their total GHG emissions. Thus, the differences of GHG emissions among the energy sources are rather small between the greenhouse in Sweden and the greenhouse in the Netherlands.
Comparing greenhouse cultivation and VF with lighting efficiency of 52% each running with coal power can be observed that VF produces 2.5 – 7 times higher GHG emissions depending on the location. When comparing the same systems running with hydropower, VF produces 15-27% of the GHG emissions produced by a greenhouse. However, if the energy source is assumed to be hydropower, for example, the GHG emissions for VFs 52 would be 15%- 30% of the GHG emissions emitted by the greenhouses depending on the location.
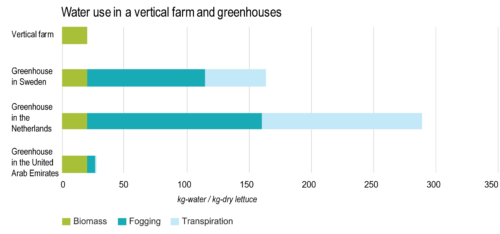
In the study, vertical farms are assumed to be closed systems in terms of water use while in greenhouses the rate of ventilation has a high impact on water use. In other words, in VF all the water put into the system is converting to biomass while in greenhouses part of the water consumes to fogging and transpiration. In greenhouses the water use seems to depend highly on the location: Greenhouses in Sweden and the Netherlands use fogging as a cooling method instead of an air conditioner and the humidity level in the greenhouse is managed with ventilation. In the United Arab Emirates where water is more scarce compared to the other referred locations, water is not used for cooling.
The drastic difference between greenhouse cultivation and vertical farming is the land use efficiency (Figure 9). The VF with 6 layers to cultivate crops on yields more than seven times more yield compared to the semi-closed greenhouse in the UAE and more than 12 times more yield compared to the conventional greenhouses in Sweden and the Netherlands. According to Kikuchi et al. (2018), the yield capacity of open field cultivation is only 1.2 % of the yield capacity of the VF.
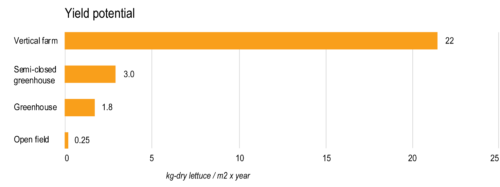
Conclusion
The source of energy has obviously the most significant effect on the GWP of different cultivation systems. As the GWP for coal power is around 70 times higher compared to nuclear of wind power, the differences between the locations, LED efficiencies and event the difference between the cultivation methods (VF and greenhouse) are rather small. However, as comparing the VF and greenhousing from the perspective of energy intensity, it is easily observed that greenhouse cultivation is less energy intensive than VF even in relatively harsh climate conditions with limited sunlight, extreme temperatures or both.
While water use efficiency is assumed to reach 100% for VFs, in greenhouses water use is highly dependent on the cooling method and ventilation rate. In areas affected by water scarcity, it is possible to perform greenhouse cultivation with almost the same water use as in vertical farming. Therefore, farming vertically as itself does not offer a solution for areas affected by water scarcity but the controlled air ventilation does which is applicable also for greenhouses.
Extremely efficient land use is the advantage which marks vertical farming out of single-story systems. A six-storey VF can achieve higher than a ten-fold efficiency in land use compared to a conventional GH and a 100-fold efficiency compared to open field cultivation. How far this among the other advantages are able to compensate for the high energy consumption, should be further studied.
Eero Hallikainen is a master’s student in the programme of Water and Environmental Engineering. The topic of his thesis was Life Cycle Assessment on Vertical Farming which he ended up via Greenhouse pre-incubator program and an internship in Ruralia Institute, University of Helsinki.
Sources
Graamans, L; Baeza, E; van den Dobbelsteen, A; Tsafaras, I; Stanghellini, C. 2018. Plant factories versus greenhouses: Comparison of resource use efficiency. Agricultural Systems. Vol. 160:November, pp. 31–43. Available: DOI: 10.1016/j.agsy.2017.11.003
Intergovernmental Panel of Climate Change (IPCC). 2014. Climate Change 2014: Synthesis Report., Climate Change 2014, pp. 2-26. Available: DOI: 10.1256/004316502320517344
ISO 14040:2006. Environmental management – Life cycle assessment – Principles and framework
ISO 14040:2006. Environmental management – Life cycle assessment – Requirements and guidelines.
Kikuchi, Y.; Kanematsu, Y.; Yoshikawa, N.; Okubo, T.; Takagaki, M. 2018. Environmental and resource use analysis of plant factories with energy technology options:
A case study in Japan. Journal of Cleaner Production. Vol. 186, pp. 703–717. Available: DOI: 10.1016/j.jclepro.2018.03.110
Kozai, T. 2013. Resource use efficiency of closed plant production system with artificial light: Concept, estimation and application to plant factory. Proceedings of the Japan Academy, Vol 89:10, pp. 447–461. Available: DOI: 10.2183/pjab.89.447
Kozai, T. and Fujiwara, K. 2016. LED Lighting for Urban Agriculture. Available: DOI: 10.1007/978-981-10-1848-0
USDA. 2018. Available: https://www.usda.gov/media/blog/2018/08/14/vertical-farming-future